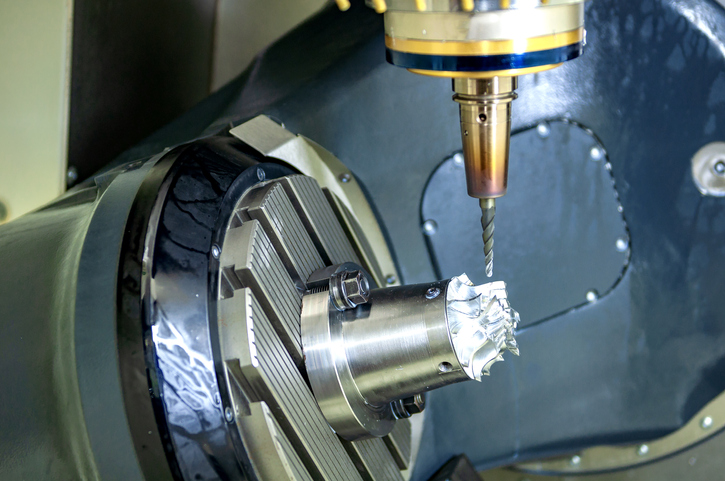
Most designers and purchasers have heard of CNC machining. Some have heard “precision” tacked on as well. But people looking for these services — especially those considering an upgrade from manual machining — might not understand what each term truly means. Or what they’re truly getting out of a precision machine product.
If you need to optimize a mission-critical component, it’s great to know: What is CNC machining equipment? And what is precision machining? Is there even a difference?
With this knowledge in hand, you can decide whether your project requires a precision machining shop to take your idea to the finish line.
What Is Precision Machining?
Precision machining is specified by OEMs (original equipment manufacturers) to transform materials. A precision machinist is someone who takes a raw piece of material — often metal — and shaves it down to a desired shape.
Precision machining uses Computer-Aided Manufacturing (CAM) or Computer-Aided Design (CAD). This provides the most precise measuring and cutting to exact specifications. Precision machining is used to make a range of objects:
- Surgical instruments
- Aerospace components
- Solar and wind components
- Much more
While drill presses and lathes are used in combination, the latest technology with precision machining involves high-speed robotics too.
History of Machining
Machining dates back to 700 B.C. Unfortunately there were no buttons to push back then — a manual lathe was the instrument of choice. Late in the 1700s A.D, steam power made things much easier. By adding steam, machining became automated and the Industrial Revolution kicked into full gear with mass production. The manufacturing of machine tools on a large scale upgraded steel-making processes everywhere, along with a host of other innovations.
Since then, modern machining has gone from using punch cards in the 1940s to actual computer technology for programming that we use today.
How Does CNC Machining Work?
To keep close tolerances in today’s manufacturing, many companies turn to Computer Numerical Control (CNC) equipment. CNC machining is the basic process of machining via, well, machine instead of manual labor.
In this type of machining, the operator uses CAD or CAM software to produce a file read by the CNC machine. From here, the machine handles the actual machining mechanically.
So, what’s the difference between CNC machining and precision machining? It’s in the name, really. Precision machining is set to a higher standard.
- The tolerance standard of a CNC machine is typically 0.008” or 0.005”
- The tolerance standard in precision machining can be as close as 0.0001”
Doesn’t sound like much, does it? But that little boost provided by precision machining technology allows your manufacturer to make complex shapes impossible with standard CNC or hand machining. In aerospace and medical device machining, meeting exact specs can be a life-or-death matter.
Types of CNC Machines
Along with the basic CNC machining and precision machining setups, there are other, more specialized types of machines. To optimize your project, consult with the manufacturer about its capabilities and recommendations.
The various types of CNC machine capabilities include:
- 3-axis CNC machining
- CNC milling
- CNC turning
- Multi-axis CNC machining
- Indexed CNC machining 3+2 axis
- Indexed 5-axis CNC milling
- 5-axis CNC machining
- Continuous 5-axis CNC milling machining
- Mill turning CNC centers
Turning and Milling
Two of the most common uses of CNC machining are turning and milling.
Turning uses a cutting tool, such as a late, to reduce the diameter of a surface in a cylindrical manner. Turning is great for prototypes and short-run volumes.
Milling uses a milling cutter or multipoint cutter tool to create a flat or stepped surface. CNC milling is usually best suited as a secondary operation to add finishing features on a custom design.
Capabilities of CNC Machining/Precision Machining
When you choose next-level machining, take into account the order volume you need. Some vendors gladly handle 1,000-part releases, or even just a single prototype for eventually larger-scale production. ACNC machining house might only take much larger volumes.
Another bonus with some vendors is the presence of in-house toolmakers that are ready to tackle any shape design. We always recommend allowing some flexibility in your design — in the end, the manufacturer is always going to know best what will work and what won’t come production time.
Materials Used in Precision Machining
With precision machining technology, there are many different types of materials that are used — much more than some other processes, such as powder metallurgy.
These materials include:
- Steel
- Bronze
- Graphite
- Glass
- Plastic
- Brass
- Titanium
- Other metals
The abilities of grinders, saws, and milling machines to effectively and efficiently transform these raw materials into finished products is why high precision CNC machining is so sought-after in several industries.
How Precise Do You Need to Be?
If you need to take your design to the next level, standard CNC machining may not be enough. Precision machining can be a game changer by allowing you to reshape your design and keep the close tolerances your industry demands. If you have more questions about precision machining and which operations will work best with your design, let us know!